Quick Summary:
AI-powered warehouse automation is transforming logistics by improving efficiency, accuracy, and scalability. Technologies like machine learning (ML), computer vision, and robotics optimize operations, from real-time inventory tracking and intelligent sorting to automated picking, packing, and quality control. AI-driven robots, AMRs, and AGVs streamline workflows, reduce errors, and enhance fulfillment speed. Predictive analytics, digital twins, and AI-powered WMS further optimize the supply chain, giving businesses a competitive edge in cost, agility, and operational efficiency.
Warehouses are the backbone of supply chain logistics, but rising e-commerce demand and global disruptions have exposed the inefficiencies of traditional systems. Manual sorting, outdated inventory tracking, and slow fulfillment create costly delays and errors.
AI in warehouse automation is transforming logistics by integrating Machine Learning (ML), Computer Vision, and robotics, enabling real-time inventory tracking, predictive demand forecasting, and automated sorting. Industry leaders like Amazon, UPS, and FedEx are already leveraging AI-driven warehouse systems to boost efficiency, reduce labor costs, and optimize storage.
The message is clear that AI in supply chain logistics isn’t just an upgrade it’s the key to future-proofing operations. Businesses that embrace AI-powered automation now will lead the charge, benefiting from scalability, accuracy, and unmatched operational agility.
How AI is Reshaping Warehouse Automation and Enhancing Efficiency?
Traditional warehouses, reliant on manual processes and barcode tracking, struggle with inefficiencies and rising costs. With e-commerce growth and the demand for faster deliveries, outdated WMS can’t keep up.
The solution? AI-powered warehouse automation.
By integrating Machine Learning, robotics, and real-time analytics, AI transforms warehouses into self-optimizing ecosystems that adapt, improve, and operate at peak efficiency. Unlike static automation, AI enhances accuracy, speed, and responsiveness redefining the modern logistics.
Let’s explore the key AI technologies revolutionizing warehouse operations.
1. Machine Learning (ML) for Predictive Analytics & Demand Forecasting
Balancing inventory is a constant challenge like overstocking ties up capital, while understocking leads to delays. Traditional forecasting is often reactive, increasing risks and inefficiencies.
AI-powered Machine Learning transforms inventory management with real-time predictive analytics. By analyzing sales trends, supplier lead times, customer behavior, and external factors like weather and economic shifts, ML creates dynamic, data-driven forecasts.
Unlike static models, ML adapts continuously, improving accuracy over time. This enables warehouses to optimize stocking strategies, reducing waste, preventing shortages, and enhancing efficiency.
Key AI-Driven Predictive Models Used
Time Series Forecasting
ML-based Time Series Forecasting analyzes historical sales data to identify patterns and trends in demand fluctuations. By continuously learning from past trends, AI algorithms can accurately predict future sales cycles, enabling smarter inventory planning.
For example, AI models can anticipate peak demand periods (such as holiday seasons or back-to-school shopping) and adjust stock levels accordingly to prevent supply shortages or overstocking.
Anomaly Detection
AI-driven Anomaly Detection helps warehouses identify unexpected demand spikes, supplier disruptions, or unusual inventory movements in real-time.
By detecting early warning signs of inventory mismatches or supply chain inefficiencies, AI ensures that warehouses can proactively address potential issues before they escalate into full-scale disruptions.
For instance, if a supplier delay is detected, AI can recommend alternate sourcing options to prevent bottlenecks in the supply chain.
Automated Replenishment Models
Automated replenishment powered by AI dynamically adjusts restocking levels based on real-time predictions. Instead of manually setting reorder points, AI-driven models continuously track inventory movements and trigger automated purchase orders when stock levels reach critical thresholds.
These models also factor in supplier lead times, transit durations, and fluctuating demand, ensuring that warehouses never experience stockouts or overstock situations.
Business Impact of AI-Driven Predictive Analytics
Reduces Unnecessary Inventory Holding Costs
By accurately forecasting demand, warehouses no longer need to overstock inventory as a precautionary measure. This significantly reduces storage costs, prevents capital from being tied up in excess inventory, and optimizes warehouse space utilization.
Prevents Supply Chain Disruptions
AI-driven demand forecasting ensures that supply chain managers receive early alerts about potential stock shortages or delays, allowing them to take proactive measures to mitigate risks.
By eliminating last-minute scrambling for inventory, businesses can maintain smooth operations and prevent revenue losses caused by supply chain inefficiencies.
Enables Real-Time Inventory Adjustments
Unlike traditional rule-based inventory systems, AI-driven forecasting allows warehouses to dynamically adapt to market conditions, customer demand, and external disruptions. This real-time adaptability ensures that businesses remain agile and responsive in a fast-changing supply chain landscape.
Real World Use-case of Predictive Analysis
Leading retailers like Amazon, Walmart, and Alibaba use AI-driven predictive analytics to optimize inventory across global warehouses. By integrating real-time demand forecasting into Warehouse Management Systems (WMS), they ensure precise stock availability while minimizing waste.
Amazon’s AI automates replenishment, pre-positioning inventory for faster deliveries, while Walmart leverages AI to predict regional buying trends, preventing stockouts during peak seasons.
2. Computer Vision for Smart Sorting and Quality Control
Manual sorting and quality control are slow, error-prone, and unsustainable for today’s high-volume warehouses. Misplacements, sorting errors, and undetected damages impact order accuracy, efficiency, and customer satisfaction.
AI-driven Computer Vision automates these processes with real-time adaptability and precision. By analyzing images and video feeds, AI detects defects, categorizes products, and ensures accurate sorting by minimizing the errors with minimal human intervention.
As e-commerce scales, Computer Vision is becoming essential for modern warehouse automation, ensuring speed, accuracy, and reliability in logistics.
Transforming Warehouse Operations with AI-Driven Visual Intelligence
AI-powered Computer Vision systems use a combination of high-resolution cameras, deep learning models, and real-time analytics to enhance warehouse sorting and quality control.
Identifies Products Using AI-Driven Image Recognition
Instead of relying solely on barcodes and QR codes, Computer Vision systems use advanced image recognition algorithms to visually identify and categorize products based on their shape, size, texture, and packaging.
- This eliminates errors caused by damaged or missing labels and allows warehouses to track inventory more accurately.
- AI can differentiate between nearly identical products, ensuring that the correct item is always picked, sorted, and packed.
- Some systems integrate Optical Character Recognition (OCR) to read and verify text-based labels, further improving accuracy in categorization.
Detects Damaged or Mislabeled Items in Real-Time
Defective, damaged, or mislabeled products often make their way into customer shipments, leading to returns, refunds, and reputational damage.
- AI-powered visual inspection models instantly scan each item to detect scratches, dents, misprints, or defects before the product is processed further.
- Machine learning algorithms compare each item against predefined quality standards, ensuring that only defect-free products move forward.
- AI enables real-time flagging of anomalies, directing faulty items for manual inspection or automated removal, preventing losses due to poor quality control.
Ensures Precise Sorting and Automated Routing
Sorting errors lead to delayed shipments, misrouted orders, and increased return rates. Computer Vision eliminates these inefficiencies by enabling:
- Automated conveyor-based sorting – AI systems track each package and ensure it reaches the correct bin, reducing human handling errors.
- Dynamic bin allocation – AI determines the best sorting category for each product based on its destination, size, or fulfillment priority.
- Real-time data updates – Warehouse management systems (WMS) receive instant updates on sorted inventory, improving visibility and efficiency.
Business Impact of AI-Powered Sorting and Quality Control
Eliminates Sorting Errors and Improves Order Accuracy
With automated, AI-driven classification and routing, the chances of products being sent to the wrong location or warehouse bin are drastically reduced. This enhances operational accuracy, ensuring that:
- Orders are fulfilled correctly the first time.
- Customer complaints and return rates decrease.
- Less time and labor are spent correcting sorting mistakes.
Enables High-Volume Processing with Minimal Labor
Manual sorting processes cannot scale to meet the demands of modern supply chains. AI-powered Computer Vision allows warehouses to:
- Process thousands of items per hour, far exceeding human capabilities.
- Reduce dependence on manual labor, cutting costs while increasing throughput.
- Improve warehouse efficiency, making fulfillment operations faster and more agile.
Reduces Operational Costs and Enhances Productivity
By automating visual inspection, sorting, and quality control, warehouses reduce labor-intensive tasks, which translates into:
- Lower labor costs, as fewer employees are required for manual sorting.
- Faster processing speeds, leading to quicker order fulfillment and reduced lead times.
- Fewer product returns due to defective or mislabeled shipments, improving overall profitability.
Real-World Use Cases
FedEx: AI-Powered Sorting at Scale
FedEx employs AI-driven Computer Vision and robotic sorting systems to process millions of packages daily. These automated conveyor-based systems use AI-powered cameras to:
- Instantly classify packages based on their destination, size, and shipping priority.
- Detect mislabeled or damaged items and reroute them for correction.
- Reduce sorting time by up to 30%, ensuring faster package movement and on-time deliveries.
UPS: Optimized Logistics Through AI Vision Systems
UPS leverages Computer Vision and deep learning algorithms in its smart logistics hubs to:
- Optimize sorting and routing, ensuring more efficient last-mile deliveries.
- Reduce sorting errors by 99%, improving customer satisfaction.
- Minimize manual inspection requirements, allowing employees to focus on higher-value tasks.
3. AI Powered Robotics Including AMRs AGVs and Robotic Arms
AI-powered warehouse robots have transitioned from innovation to necessity, automating critical tasks like picking, packing, sorting, and transportation with unmatched precision. By integrating Artificial Intelligence (AI), Machine Learning (ML), and Computer Vision services, these robots optimize inventory movement, streamline traffic flow, and adapt workflows in real time. The result? Faster fulfillment, reduced manual effort, and highly efficient warehouse operations.
Let’s explore the different types of AI-powered warehouse robots and their game-changing capabilities.
Autonomous Mobile Robots (AMRs) – Self-Navigating Warehouse Assistants
Autonomous Mobile Robots (AMRs) revolutionize warehouse movement by autonomously transporting inventory between storage areas, picking zones, and fulfillment stations. Unlike traditional conveyor belts or manually operated carts, AMRs use AI-powered navigation systems to adjust routes dynamically, avoid obstacles, and optimize traffic flow in real time.
AI-Powered Path Planning
AMRs use Reinforcement Learning (RL) to map and optimize their routes within a warehouse. By continuously learning from past movements, they identify the shortest and most efficient paths, reducing travel time. Their AI algorithms adapt in real-time to changing warehouse layouts, shelving additions, or operational bottlenecks. Additionally, energy-efficient routing ensures AMRs conserve battery life by selecting routes that minimize unnecessary movements.
Multi-Robot Coordination
Large warehouses deploy hundreds of AMRs, and AI ensures that they move seamlessly without collisions or congestion. AMRs communicate with each other and Warehouse Management Systems (WMS) to evenly distribute tasks, ensuring no single robot is overburdened. If a particular zone becomes congested, robots adjust their routes dynamically to maintain workflow efficiency. This multi-robot synchronization maximizes throughput while avoiding downtime due to traffic jams.
Dynamic Work Allocation
AMRs use AI-driven task prioritization to determine which inventory needs to be transported first. High-priority orders (such as same-day deliveries) take precedence, while less urgent stock movements are scheduled accordingly. AMRs also track real-time warehouse conditions, avoiding aisles with high congestion. Furthermore, battery-aware operations allow AMRs to autonomously recharge when power is low, ensuring continuous operation without human intervention.
Why It Matters: AMRs significantly increase warehouse agility, reduce reliance on human intervention, and improve inventory transport speed, leading to faster fulfillment cycles and greater operational efficiency.
Automated Guided Vehicles (AGVs) – Heavy Load Transport Specialists
Automated Guided Vehicles (AGVs) specialize in transporting heavy loads across warehouses, eliminating the need for manual forklifts. Unlike AMRs, AGVs follow predefined routes, making them ideal for structured environments with high-volume, repetitive transport needs.
AI Navigation Systems
AGVs employ Simultaneous Localization and Mapping (SLAM), an AI-driven technology that allows them to create and update maps of warehouse layouts in real-time. This capability enables AGVs to adjust their routes dynamically based on warehouse changes such as new shelving units, obstacles, or temporary storage adjustments. The AI-driven navigation system also ensures collision-free movement, reducing operational risks and improving transport efficiency for bulk inventory handling.
Real-Time Traffic Optimization
AI continuously monitors warehouse traffic density and AGV movement patterns, adjusting paths in real-time to prevent congestion in high-traffic areas. If a route becomes overcrowded, AGVs will automatically reroute or adjust their speed to maintain smooth traffic flow. Additionally, AI prioritizes fragile or time-sensitive shipments, ensuring perishable or high-value inventory is transported with minimal delays.
Integration with Warehouse Management Systems (WMS)
AGVs integrate seamlessly with WMS platforms to automate scheduling, optimize transport routes, and synchronize with other warehouse robots like AMRs and robotic arms. These integrations allow real-time operational monitoring, enabling warehouse managers to track AGV performance, detect inefficiencies, and optimize warehouse logistics dynamically. WMS-enabled AGVs also provide predictive maintenance alerts, preventing breakdowns that could disrupt supply chain operations.
Why It Matters: AGVs eliminate the need for manual forklifts, reducing labor costs, increasing warehouse safety, and ensuring efficient transport of heavy loads without human intervention.
Robotic Arms AI Precision for Picking and Packing
AI-powered robotic arms replicate human dexterity, performing complex picking, packing, and sorting tasks with precision and consistency. These robotic arms use Computer Vision, Deep Learning, and Adaptive Gripping Technology to handle diverse product types and packaging requirements.
Computer Vision-Assisted Object Recognition
AI-powered robotic arms leverage advanced image recognition and machine learning algorithms to identify and sort products with precision. Instead of relying solely on barcodes or RFID tags, robotic arms recognize product shape, color, texture, and labeling details. This enables them to differentiate between similar-looking items, ensuring correct product identification during sorting and packing processes. Additionally, they can detect irregular packaging or mislabeled goods, preventing shipping errors.
Adaptive Gripping Technology
Robotic arms are equipped with adaptive grippers that adjust grip strength based on object fragility and weight. AI-powered feedback systems allow them to detect pressure resistance and modify grip force accordingly, ensuring that fragile items (such as glassware or electronics) are handled delicately, while heavier items are securely grasped. These grippers self-learn from past handling and refine their performance over time, reducing breakage rates and improving overall packing efficiency.
Collaborative Robotics (Cobots)
Unlike traditional robots that work in isolation, Cobots (Collaborative Robots) are designed to operate safely alongside human workers. These AI-enhanced robotic arms assist warehouse employees by handling repetitive, labor-intensive tasks, such as heavy lifting and precise assembly-line operations. Real-time human detection algorithms ensure Cobots stop or adjust movement if they sense human proximity, enhancing workplace safety while increasing operational efficiency.
Why It Matters: AI-powered robotic arms reduce manual errors, improve speed and accuracy in picking/packing, and enhance worker safety by eliminating physically demanding tasks.
Business Impact of AI-Powered Warehouse Robotics
Increases Order Fulfillment Speed by Up to 300%
AI-driven robots can process orders three times faster than human workers by automating sorting, picking, and packing.
- Shorter processing times mean faster deliveries and improved customer satisfaction.
- Warehouses can handle higher order volumes without increasing labor costs.
Reduces Dependency on Manual Labor, Cutting Operational Costs
By automating repetitive warehouse tasks, AI-powered robotics reduce labor costs by eliminating human-intensive processes.
- Employees focus on high-value tasks like logistics planning and quality control instead of manual stock movement.
- Reduced reliance on physical labor leads to fewer workplace injuries and lower insurance costs.
Improves Warehouse Efficiency and Accuracy in High-Volume Operations
AI-powered robots enhance warehouse accuracy and operational agility by:
- Minimizing sorting errors, reducing product misplacements.
- Enabling scalability, allowing warehouses to handle seasonal demand surges without operational slowdowns.
- Providing real-time inventory tracking, ensuring all products are stored and retrieved efficiently.
Real-World Use Cases
Amazon: AI-Powered Warehouse Robotics at Scale
As, per reports, Amazon has integrated over 750,000 AI-driven robots into its fulfillment centers to enhance logistics operations. These robots perform tasks such as transporting packages, sorting items, and creating customized packaging. The deployment of these advanced robotic systems has significantly improved delivery times and operational efficiency.
DHL: Enhancing Efficiency with Robotic Sortation
DHL has implemented AI-powered robotic arms in its distribution centers to streamline parcel sorting processes. In a pilot program at their Atlanta facility, the robotic system demonstrated the capability to sort over 1,000 parcels per hour with near-zero error rates, averaging 3.6 seconds per package. This implementation has led to increased efficiency and reduced error rates in their operations.
Generative AI in Warehouse Management for Adaptive Optimization
Warehouses are evolving beyond automation into self-optimizing ecosystems. While traditional AI streamlines operations through predictive analytics and robotics, Generative AI takes a proactive approach, dynamically reshaping warehouse layouts, schedules, and workflows in real-time based on incoming data.
How Generative AI Works in Warehouse Optimization?
Warehouse Layout Optimization
A well-organized warehouse minimizes travel time, prevents congestion, and optimizes storage space. Generative AI analyzes inventory flow, demand patterns, and retrieval frequency to create adaptive layouts that evolve as needs change. Instead of static, human-designed configurations, AI constantly reshuffles storage placements, reducing wasted space and increasing efficiency.
Example: AI might reposition high-demand items closer to dispatch zones during peak seasons, cutting retrieval time by up to 40%.
AI-Powered Scheduling
Workforce management is crucial for handling fluctuating order volumes efficiently. Generative AI automates labor allocation by analyzing order trends, workload distribution, and shift capacities to create an optimal schedule. It assigns tasks dynamically, ensuring even workload distribution across human workers and robots.
Example: During high-demand hours, AI increases staffing in packing zones while redirecting AMRs to replenish stock in low-traffic areas.
Dynamic Workflow Adjustments
Unlike static automation rules, Generative AI continuously adapts warehouse workflows. It responds to real-time warehouse conditions, adjusting operations on the fly to prevent bottlenecks and maximize efficiency.
Example: If one picking station becomes overloaded, AI reroutes tasks to less busy zones, preventing delays and optimizing throughput.
Why Generative AI Matters?
Modern warehouses need more than automation they need adaptability. Generative AI dynamically optimizes layouts, schedules, and workflows in real time, adjusting to demand shifts, resource availability, and supply chain disruptions.
By enabling self-adjusting operations, AI enhances efficiency, speed, and resilience, ensuring warehouses stay agile in a rapidly evolving market.
Self Optimizing AI for Real Time Warehouse Adaptation
Traditional WMS require manual adjustments, but Generative AI autonomously detects inefficiencies and optimizes layouts, workflows, and resource allocation.
By analyzing real-time inventory movement and order flow, AI restructures storage zones, reroutes AMRs, and reassigns workers which helps in preventing bottlenecks and ensuring peak efficiency. This self-optimizing system enables faster fulfillment, minimal downtime, and seamless adaptation to demand shifts.
AI Optimizing Warehouse Storage to Reduce Wasted Space by 30%
Traditional warehouses waste space with fixed storage setups. Generative AI optimizes storage dynamically by analyzing density, turnover rates, and retrieval frequency.
AI rearranges inventory placement, grouping fast-moving items for quick access and shifting low-demand stock, maximizing efficiency. This reduces wasted space, boosts storage capacity, and minimizes expansion costs.
AI Scaling Warehouses to Adapt to Demand Surges and Supply Chain Shifts
Warehouses must adapt to fluctuating demand, especially during peak seasons, product launches, or disruptions. Generative AI forecasts demand shifts and adjusts workflows to prevent delays, stockouts, or overstocking.
AI pre-allocates space for high-demand items and dynamically reprioritizes inventory replenishment to avoid fulfillment disruptions. This ensures agile, efficient, and responsive warehouse operations in any market condition.
Real-World Use Cases
As per reports, DHL uses Generative AI-powered digital twins to simulate warehouse operations before implementing changes, resulting in a 40% reduction in operational bottlenecks. By digitally testing optimizations before applying them, DHL ensures minimal disruptions and maximum efficiency gains.
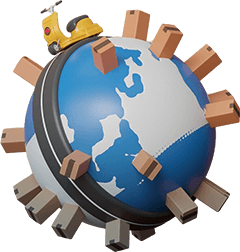
Searching for Supply Chain IT Solutions?
Optimize supply chain and warehousing with our cutting-edge solution – enhancing efficiency, reducing costs, and improving workflows with agility and transparency.
The Benefits of AI-Driven Warehouse Optimization
AI-driven warehouse optimization is redefining logistics, enabling warehouses to operate faster, smarter, and more efficiently than ever before. By automating order fulfillment, inventory tracking, and process management, AI minimizes inefficiencies and helps businesses scale effortlessly.
Let’s explore how AI is transforming warehouse operations:
Faster Order Fulfillment
AI-Driven Picking and Sorting
Traditional order fulfillment relies on manual labor, leading to delays and errors. AI-powered robotics, Autonomous Mobile Robots (AMRs), and AI-driven conveyor systems accelerate picking, sorting, and packing, reducing processing times by up to 70%.
Smart Inventory Allocation
AI dynamically assigns storage locations based on product demand and retrieval frequency. This means high-demand products are stored closer to picking zones, reducing travel time for workers and robots, ensuring lightning-fast order fulfillment.
Impact: Businesses can process more orders per hour, meeting same-day and even one-hour delivery expectations.
Lower Costs
Reduced Labor Expenses
AI-driven automation lowers dependency on manual labor by automating repetitive tasks like picking, sorting, and transportation. This leads to cost savings on wages, overtime, and human error corrections.
Optimized Energy & Space Usage
AI reduces operational costs by optimizing warehouse layouts and energy consumption. For example, smart AI systems adjust lighting and temperature based on real-time activity levels, cutting energy waste.
Impact: Companies see a 20-30% reduction in overall operational costs, making AI-powered warehouses more cost-efficient than traditional ones.
Data-Driven Accuracy
Elimination of Human Errors
AI-powered inventory tracking and barcode scanning ensure 99.9% accuracy in stock levels. AI prevents overstocking, understocking, and misplaced inventory, reducing costly mistakes in order fulfillment.
Real-Time Insights & Predictive Analytics
AI continuously monitors supply chain disruptions, product demand, and stock levels, allowing warehouses to make real-time decisions and prevent shortages or excess stock.
Impact: With AI, warehouses operate with pinpoint accuracy, reducing return rates and improving customer satisfaction.
Scalability & Resilience
Adapts to Market Fluctuations
AI-powered warehouse systems scale effortlessly during peak demand seasons, like Black Friday or holiday sales, by automatically adjusting labor, space, and resources.
Supply Chain Resilience
AI predicts and mitigates risks caused by supply chain disruptions. If a supplier delay occurs, AI reconfigures stock allocation to ensure uninterrupted operations.
Impact: AI-driven warehouses remain agile and competitive, adapting to market shifts without disruptions.
Overcoming Challenges in AI Driven Warehouses Including Costs Ethics and Security
AI-driven warehouse automation, offers efficiency, speed, and cost savings, but integration comes with challenges. Businesses must navigate financial, ethical, and security concerns to ensure a smooth transition.
Let’s explore the key hurdles in adopting AI-powered warehouse solutions.
High Implementation Costs and Integration Challenges
Upgrading to AI-driven automation requires substantial capital investment in robotics, sensors, AI software, and cloud-based infrastructure. Beyond hardware costs, integration with existing Warehouse Management Systems (WMS) and Enterprise Resource Planning (ERP) platforms can be complex, requiring significant time and technical expertise.
- Infrastructure Upgrades – Traditional warehouses may need a complete overhaul to support AI-powered robotics and IoT-enabled tracking. This includes cloud migration, high-speed data networks, and sensor-enabled storage systems.
- Software and Data Integration – AI relies on vast amounts of data to function optimally. Companies must ensure seamless data synchronization between legacy systems and AI models, avoiding inconsistencies that can impact decision-making.
- Ongoing Maintenance & Scalability – AI-powered robots and machine learning models require continuous monitoring, updates, and recalibrations to adapt to changing warehouse layouts and business needs.
Key Consideration: Companies must balance the long-term return on investment (ROI) against initial implementation costs, ensuring AI solutions align with business goals and operational capacity.
Ethical Considerations and Workforce Impact
The shift toward AI-powered warehouses raises concerns about job displacement, workforce upskilling, and the ethical responsibility of AI-driven decision-making. While automation reduces dependency on manual labor, it also transforms job roles rather than eliminating them outright.
- Workforce Displacement vs. Augmentation – AI automates repetitive tasks, but human oversight is still needed for robotic maintenance, AI model training, and workflow optimization. Businesses must focus on reskilling employees to transition into AI-supported roles rather than outright job replacement.
- Bias in AI Decision-Making – AI algorithms can inadvertently reinforce biases present in historical warehouse data, affecting workforce scheduling, supplier relationships, and even inventory prioritization. Ensuring fair and unbiased AI decision-making is crucial.
- Regulatory Compliance – As AI adoption increases, businesses must adhere to emerging AI governance frameworks and labor laws that address ethical concerns in automated warehouse operations.
Key Consideration: Instead of replacing workers, businesses should invest in AI training programs to create a workforce that collaborates with AI rather than competes against it.
Cybersecurity Concerns in AI-Powered Logistics
AI-driven warehouse automation relies on interconnected IoT devices, cloud networks, and real-time data processing, making it a potential target for cyberattacks, data breaches, and AI manipulation. Without robust security measures, hackers could disrupt logistics operations, tamper with inventory data, or exploit AI decision-making vulnerabilities.
- AI Model Manipulation & Data Poisoning – Malicious actors could feed AI systems false inventory data to manipulate stock levels, disrupt fulfillment schedules, or cause delays in high-demand products.
- IoT & Network Vulnerabilities – AI-powered warehouses depend on IoT sensors, RFID scanners, and cloud-based WMS platforms. If security protocols aren’t enforced, bad actors could exploit vulnerabilities to access sensitive data or take control of automated systems.
- Regulatory Compliance & Data Protection – Businesses must align AI implementations with global cybersecurity standards such as GDPR, CCPA, and ISO 27001 to safeguard customer and operational data.
Key Consideration: Implementing multi-layered security protocols, AI model validation, and real-time anomaly detection can mitigate risks and ensure AI-powered warehouse systems remain resilient against cyber threats.
Next-Gen AI Innovations in Warehouse Automation
Warehouses are transforming into self-learning, self-optimizing ecosystems driven by AI. As supply chains demand greater efficiency, adaptability, and real-time intelligence, emerging AI technologies like Generative AI, Edge Computing, and fully autonomous warehouse ecosystems are reshaping the future of warehouse automation.
Unlike previous automation waves that focused on task-specific robots, these next-gen AI systems introduce adaptive intelligence, decentralized processing, and self-regulating workflows allowing warehouses to operate at peak efficiency with minimal human intervention.
Let’s explore the AI advancements set to redefine warehouse operations.
The Future of AI in Warehouse Automation
As AI models evolve, Generative AI services are emerging as game-changers in warehouse decision-making, workflow optimization, and adaptive logistics planning. Unlike traditional AI, which analyzes past data, Generative AI services create dynamic models to simulate warehouse scenarios and improve operational efficiency.
- AI-Generated Warehouse Layout Optimization – Generative AI simulates different warehouse configurations, identifying the most efficient storage layouts to reduce travel time for robotic pickers and human workers.
- Intelligent Demand Planning & Forecasting – Instead of simply predicting demand, Generative AI models multiple demand fluctuation scenarios and suggests optimal inventory restocking strategies.
- Adaptive Workflow Automation – AI continuously adjusts picking, packing, and replenishment workflows in real time based on traffic flow, demand shifts, and labor availability.
The Future: Generative AI will transform warehouse management from reactive to proactive, allowing warehouses to self-adjust in real time without human intervention.
Edge Computing Real-Time AI Processing for Smarter Warehouses
Traditional AI models rely on cloud-based processing, which can introduce latency issues when managing real-time warehouse operations. Edge computing solves this by processing AI algorithms directly on warehouse IoT devices, sensors, and robots, enabling instant decision-making without relying on distant cloud servers.
- Faster AI-Powered Sorting & Routing – With AI models running on-site, warehouses can make instant decisions on sorting and routing without waiting for cloud-based processing.
- Reduced Network Congestion – By offloading AI processing to edge devices, warehouses reduce the burden on cloud networks, ensuring low-latency, high-speed operations.
- Enhanced AI-Powered Cybersecurity – Edge computing enhances security by limiting exposure to cloud-based threats, ensuring warehouse data remains locally encrypted and protected.
The Future: Edge AI will make warehouse automation faster, more secure, and independent of external cloud delays enabling real-time decision-making at an unprecedented scale.
The Rise of Autonomous AI-Driven Warehouse Ecosystems
AI-powered automation is evolving beyond isolated robotic systems into fully autonomous warehouse ecosystems where robots, AI-driven software, and IoT sensors work collaboratively without human intervention.
- Self-Organizing Warehouses – AI dynamically rearranges inventory based on demand fluctuations, ensuring high-demand products are easily accessible while minimizing warehouse congestion.
- AI-Orchestrated Robotics – Instead of individual robots performing separate tasks, AI synchronizes AMRs, AGVs, robotic arms, and AI-driven forklifts to work as a unified fleet, improving operational efficiency.
- AI-Governed Supply Chain Adaptability – AI autonomously detects supply chain disruptions (like delays or shortages) and self-adjusts procurement, storage, and fulfillment strategies in response.
The Future: AI-driven warehouses will become fully autonomous ecosystems that self-optimize, self-correct, and self-scale to meet demand all without human oversight.
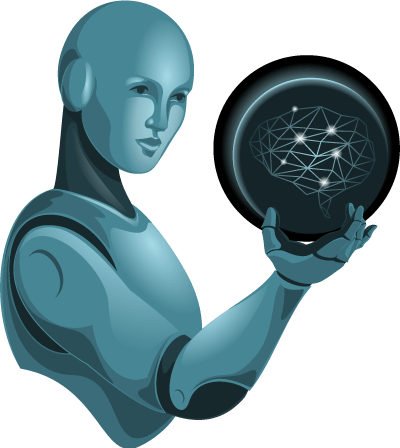
Seeking brilliance in the AI/ML universe?
Look no further!
Conclusion
AI is no longer just a tool in warehouse automation it’s the driving force behind smarter, faster, and more adaptive supply chains. From real-time inventory tracking and intelligent sorting systems to AI-powered robotics and autonomous warehouse ecosystems, AI is transforming warehouses into self-optimizing logistics hubs. As AI-driven automation continues to reduce errors, cut operational costs, and enhance efficiency, businesses that embrace these innovations will gain a competitive edge in an increasingly digital-first supply chain landscape. Now is the time for companies to invest in AI-powered logistics solutions to future-proof their warehouses, streamline operations, and stay ahead of industry shifts. The future of warehouse automation is here – intelligent, autonomous, and driven by AI.