Quick Summary:
In an industry where every second counts and inefficiency can cost millions, manufacturers are turning to AI-powered Assistants not as a novelty but as a necessity. These intelligent assistants are no longer limited to customer support they’re answering purchase order queries, surfacing real-time inventory insights, assisting sales teams, and even helping HR schedule interviews. Seamlessly integrated with ERP, CRM, and other backend systems, manufacturing Assistants are transforming real-time operations and decision-making across the value chain.
In this blog, we’re going to discuss📝
- Understanding the AI Assistants in Manufacturing
- Manufacturing Department-Wise Use Cases of Assistants on Every Floor
- Key Benefits of AI Assistant in Manufacturing
- Challenges and Considerations for AI Assistants in Manufacturing
- Real-World Examples of AI Assistants in Manufacturing
- The Future Trends of AI Assistant in Manufacturing
Even in today’s factories, the signs of traditional manufacturing are still visible like paper checklists, walkie-talkies, and manual updates. But quietly, a smarter layer is emerging. AI-powered Assistants are stepping in to simplify the complexity behind everyday operations. They’re not just basic bots but they’re built to understand real manufacturing workflows, connecting directly with ERP, CRM, and warehouse systems to answer questions, pull reports, and notify teams in real time.
Instead of jumping between tools or waiting on updates, teams now get answers instantly, through simple conversations. In this blog, we’ll look at how these Assistants are transforming key areas like procurement, inventory, sales, HR, and finance helping manufacturers work smarter, faster, and with fewer delays.
Understanding the AI Assistants in Manufacturing
When most people hear the word Assistant, they imagine a website widget answering basic FAQs. But in manufacturing, the role of an Assistant goes far deeper into the very infrastructure of how operations run.
So what exactly is an AI Assistant in manufacturing?
Manufacturing Assistants are more than just chat windows but they’re intelligent assistants built to understand the language and logic of factory operations. Unlike simple bots with canned responses, these AI Assistants connect directly to ERP, CRM, and other backend systems, allowing users to ask complex questions and get instant answers. Whether it’s a supervisor checking stock levels or HR reviewing interview schedules, the Assistant delivers fast, accurate responses no need to juggle multiple systems or wait on someone else to respond.
Types of AI Assistants in Manufacturing
To understand the value of assistants in manufacturing, it helps to know the difference between the two main types:
- Rule-Based Assistants: These operate on pre-programmed decision trees “if this, then that.” They’re useful for handling repetitive tasks like responding to standard queries or guiding users through step-by-step procedures. However, they lack flexibility and can’t handle unexpected or complex input.
- AI/NLP-Powered Assistants: These are the true game-changers. Powered by natural language processing (NLP) and machine learning, they can understand context, learn from past interactions, and handle a wide range of dynamic questions. In a manufacturing environment, they can interpret phrases like “Show me all pending purchase orders for this quarter” or “Which vendors delayed deliveries last month?” and provide immediate, relevant answers.
Integrating AI Assistants Into Manufacturing Systems
AI Assistants in manufacturing aren’t standalone tools. Their real power comes from how well they integrate into existing systems. Imagine a single interface connected to:
- ERP (Enterprise Resource Planning): For purchase orders, inventory levels, vendor data, and financial summaries
- CRM (Customer Relationship Management): To retrieve customer details, open sales orders, or support history
- OMS (Order Management System): For real-time updates on shipments, order fulfillment status, and stock movement
- IoT Systems and Sensors: To offer data-driven insights from connected devices, like temperature logs or machine usage stats
When these Assistants tap into the systems you already rely on, they act as a natural extension of your team, helping you make faster decisions without the need for dashboards, reports, or endless email chains.
Manufacturing Department-Wise Use Cases of Assistants on Every Floor
In manufacturing, every department like procurement, sales, finance, HR runs on its own tools and data. But when those systems don’t communicate well, teams waste valuable time chasing updates instead of making progress. AI-powered Assistants help fix that by acting as a smart, conversational link between people and platforms. It allow teams to pull the right information, from the right system, in real time without bouncing between dashboards or waiting on someone to reply.
The result? A smoother, faster workflow that keeps everyone aligned, no matter their role.
Procurement & Purchase
The Challenge: Procurement managers often work under tight timelines and deal with numerous vendors. Tracking purchase orders, monitoring delivery delays, and keeping an eye on raw material costs all while coordinating with other departments which can be overwhelming.
How Assistants Help: Integrated with ERP systems, Assistants give procurement teams instant access to PO status, vendor performance history, and monthly spend summaries.
Example Queries:
- “What’s the status of Purchase Order #4567?”
- “Which vendors delayed shipments last month?”
- “How much did we spend on raw materials this quarter?”
Sample Conversation: 👩💼 Procurement Lead: “Who is the vendor for PO #12345?”
🤖 Assistant: “The vendor for PO #12345 is Titan Metals. The expected delivery date is June 18th, 2025.”
Why It Matters: This eliminates guesswork, shortens the feedback loop, and helps procurement leaders make faster, data-driven decisions.
Inventory & Warehouse
The Challenge: Inventory teams constantly walk a tightrope to avoid stockouts, reduce overstocking, and keep warehouse data up to date. But warehouse management systems aren’t always the easiest to navigate.
How Assistants Help: By connecting directly to inventory databases, AI Assistants can check stock levels, show product movement, and flag low-stock items all through a simple chat interface.
Example Queries:
- “What’s the current stock level of Product XYZ?”
- “Are we running low on any critical parts?”
- “Show inventory aging report for all SKUs.”
Sample Conversation: 👨🏭 Warehouse Manager: “How many units of Product ABC are currently reserved?”
🤖 Assistant: “350 units of Product ABC are reserved for upcoming sales orders. 650 units remain available in inventory.”
Why It Matters: Teams don’t need to log into clunky systems or call across departments. They get the answers they need, fast-reducing delays and improving planning accuracy.
Sales & CRM
The Challenge: Sales reps work best when armed with real-time data. But CRM platforms often require manual digging to find what’s relevant especially during customer calls or field visits.
How Assistants Help: Sales Assistants can access and summarize sales orders, performance metrics, and customer histories on command, allowing reps to focus on closing deals instead of chasing information.
Example Queries:
- “What are the top 10 best-selling products this month?”
- “Show open sales orders for Customer XYZ.”
- “Which sales rep closed the most revenue this quarter?”
Sample Conversation: 👨💼 Sales Manager: “Any overdue payments from Client Delta Systems?”
🤖 Assistant: “Yes. Invoice #7943 for $12,800 is 15 days overdue. Due date was March 30, 2025.”
Why It Matters: The Assistant acts like a virtual assistant that’s always in sync with sales targets and customer needs, helping teams stay sharp and proactive.
Finance & Accounting
The Challenge: Finance teams rely on precise, up-to-date data. But they often get bogged down with repetitive queries or requests for reports from other departments.
How Assistants Help: AI Assistants integrated with accounting systems can answer financial queries, generate P&L statements, and surface overdue invoices without needing a full spreadsheet export.
Example Queries:
- “What’s the balance in our accounts receivable?”
- “Generate a profit and loss statement for Q2.”
- “Show me all vendor payments due this week.”
Sample Conversation: 👩💼 CFO Assistant: “Any pending payments to Johnson Electric?”
🤖 Assistant: “Yes. Two invoices totaling $22,500 are due by April 15th, 2025.”
Why It Matters: This creates a self-service finance layer across the company saving time for both finance teams and everyone else who needs financial visibility.
Human Resources
The Challenge: In manufacturing, HR teams often serve large, distributed workforces. Managing leave requests, employee records, and interview schedules across shifts can quickly become chaotic.
How Assistants Help: HR Assistants can fetch directory details, check team availability, log time-off requests, and guide employees through basic HR policies.
Example Queries:
- “Who is on leave today in the Assembly Unit?”
- “When is John’s work anniversary?”
- “How many employees joined in the last 3 months?”
Sample Conversation: 👩 Employee: “Can I take leave on April 12 and 13?”
🤖 Assistant: “You have 6 days of leave remaining. Your request has been sent to your manager for approval.”
Why It Matters: HR teams can focus on employee engagement and development not on admin part. And employees get faster answers without navigating HR portals.
Production & Manufacturing
The Challenge: Supervisors on the shop floor need up-to-the-minute information to keep production on track. Delays in communication can lead to workflow disruptions.
How Assistants Help: Production Assistants can fetch work order status, highlight rejected units, and assist in tracking daily outputs making the floor more data-responsive.
Example Queries:
- “What’s the status of Work Order #7890?”
- “How many units were produced yesterday?”
- “What’s the rejection rate on Line 3?”
Sample Conversation: 👨🏭 Supervisor: “Are there any delays in the production schedule today?”
🤖 Assistant: “Line 2 is 1 hour behind due to late raw material delivery. Adjusted estimated completion is 5:30 PM.”
Why It Matters: Assistants bring visibility without adding extra work so teams stay aligned, responsive, and efficient.
Analytics & Reporting
The Challenge: Leadership relies on up-to-date metrics, but creating reports manually is slow and often reactive.
How Assistants Help: These bots can instantly generate reports, compare performance metrics, and even visualize trends from data collected across departments.
Example Queries:
- “Show me sales vs. target for this quarter.”
- “What are our top 5 operational expenses this month?”
- “Generate a dashboard of department-wise costs.”
Sample Conversation: 👨💼 Operations Head: “Give me a breakdown of costs by department for March.”
🤖 Assistant: “Finance: $45K | Procurement: $38K | Production: $72K | Sales: $31K | HR: $18K”
Why It Matters: You don’t have to dig through spreadsheets anymore just ask, and the Assistant gives you the answer right away.
System Access & Admin (IT/Admin)
The Challenge: IT and Admin teams are often overwhelmed by basic access requests and system audits.
How Assistants Help: Assistants automate IT support tasks such as tracking user logins, handling password policy updates, and assisting with access control.
Example Queries:
- “Who accessed the ERP system in the last 24 hours?”
- “Are there any failed login attempts?”
- “Update the password policy for all users.”
Sample Conversation: 👨💻 IT Admin: “Show me user roles for Employee ID #4532.”
🤖 Assistant: “Employee #4532 (James) is assigned as ‘Procurement Analyst’ with access to ERP-Purchasing Module only.”
Why It Matters: IT teams get fewer interruptions. Employees get faster responses. And the organization becomes more secure and efficient in the process.
Key Benefits of AI Assistant in Manufacturing
We’ve seen how AI chatbots can assist across departments from procurement to HR. But beyond individual tasks and queries, what do these smart assistants actually bring to the table for manufacturers?
Turns out, quite a lot.
Let’s explore the real, measurable advantages that come from integrating AI chatbots into the manufacturing ecosystem not as just another software tool, but as a reliable digital teammate.
Enhanced Operational Efficiency
Think of the time saved when a purchase order doesn’t require five emails, or when a manager can check real-time stock levels without opening a dozen tabs. That’s efficiency not in theory, but in practice.
AI Assistants eliminate the slow, manual steps that often bottleneck daily operations. Whether it’s checking vendor delivery status or summarizing financial KPIs, what once took minutes (or hours) now takes seconds.
And since Assistants work 24/7, they handle repetitive queries at scale… no breaks, no delays.
Real-Time Data Access
Manufacturing is full of moving parts. From fluctuating inventory levels to dynamic production schedules, having outdated information is a quick way to lose control.
Assistants connected to ERP, CRM, and other backend systems offer live insights instantly. Need to know which vendors delayed shipments last month? Just ask. Want to check which team member is on leave today? It’s a message away.
And here’s the best part: the information doesn’t just come faster but it comes from the source of truth. That’s critical for confident, data-driven decision-making.
Reduced Human Error
Manual tasks often come with mistakes like typos in invoices, misread stock reports, or forgotten follow-ups. Assistants drastically reduce this risk by automating workflows and standardizing how information is retrieved and shared.
By guiding users through structured queries and directly pulling from integrated systems, Assistants eliminate ambiguity. The result? Fewer errors, more consistency, and better compliance.
They’re especially helpful in regulated environments, where every step and every record matters.
Cost Savings Across Functions
Let’s be honest being efficient isn’t just about working faster, it actually helps save money. AI Assistants help reduce manual work, avoid delays, and take pressure off support teams, which can lead to big cost savings. For example:
- Fewer support tickets for IT or HR to handle
- Reduced overtime for last-minute inventory audits
- Fewer missed opportunities in sales due to slow CRM access
Improved Employee Experience
People don’t talk about this enough but it really matters. In manufacturing, employees often waste time on small tasks instead of focusing on the important work. If an Assistant can help a warehouse manager find answers quickly, they don’t need to chase different people. If HR doesn’t have to answer the same questions over and over, they can spend more time hiring and supporting employees. From the shop floor to the finance team, this makes everyone less stressed, more productive, and more likely to stay. Because at the end of the day, people do their best work when the tools they use actually help them.
Challenges and Considerations for AI Assistants in Manufacturing
Adding AI assistant to a manufacturing setup can bring major improvements but it’s not always plug-and-play. Like any new technology, there are real-world challenges to think about before going live.
Here’s what manufacturers should know upfront, along with a few things to keep in mind when planning a successful rollout.
Legacy System Integration
Many manufacturers still use older software especially for ERP, finance, or warehouse operations. These systems were built years ago and don’t always “talk” easily with modern tools like AI chatbots.
This can slow down integration or require extra work behind the scenes. But that doesn’t mean you need to replace your entire setup.
Tip: Choose an assistant platform that can connect to older systems using APIs or middleware. Start with one integration at a time like your ERP and expand from there.
Data Security & Compliance
Assistants make it easy to access information, but that also means you need to think carefully about who can see what.
In manufacturing, sensitive data like vendor pricing, customer details, and employee info must be protected. You’ll also need to stay compliant with data protection rules depending on your industry and location.
Tip: Set up role-based access (so employees only see what they’re allowed to), use encryption, and make sure your chatbot provider follows strict security standards.
Model Training and Domain Adaptation
Every factory has its own way of talking like acronyms, part numbers, terms that only make sense to your team. A chatbot won’t automatically understand those things on day one.
If it gives wrong or confusing answers, your team won’t trust it and they won’t use it.
Tip: Train the chatbot using your company’s real data: documents, FAQs, past support tickets. Start small and improve over time by tracking how it performs and where it needs help.
Employee Adoption & Change Management
Even the best tech will fail if no one wants to use it.
Employees might be hesitant at first either because they’re unsure how it works or they worry it’s replacing jobs. Some might just prefer the old way of doing things.
Tip: Involve teams early. Show them how the chatbot makes their job easier, not harder. Start with a few everyday use cases, collect feedback, and improve from there. The more useful it feels, the faster it’ll be adopted.
Real-World Examples of AI Chatbots in Manufacturing
Now that we’ve explored how AI chatbots function and their value, let’s look at real-world applications where manufacturers are leveraging these tools to streamline operations and support their teams effectively.
AI Chatbots for Employee Support – Bosch
The Situation: With over 400,000 employees across more than 60 countries, Bosch needed a better way to handle repetitive HR requests and support internal teams without overwhelming their service departments.
The Chatbot Fix: Bosch introduced an internal AI chatbot (nicknamed ROB) to help employees with common HR tasks like updating bank details, finding career development resources, or getting policy information. The bot is multilingual, remembers conversation context, and adapts to how the employee is speaking. It’s available right where teams already work, like Microsoft Teams.
The Impact: The chatbot is now live in 25+ countries, helping teams get quick answers without waiting on HR. It’s reduced support ticket volume, improved response times, and allowed HR staff to focus more on strategic work like hiring and culture-building instead of answering the same questions every day.
AI Chatbots for Customer Support – Lippert
The Situation: Lippert, a global supplier in the caravanning, marine, and rail industries, was handling thousands of customer support requests and many involving detailed questions about part pricing, availability, or tracking orders. These queries often required specialized product knowledge and led to long response times, creating pressure on the support team and slowing down the customer experience.
The Chatbot Fix: To reduce this load and speed up service, Lippert implemented an AI-powered chatbot to handle key use cases in real time. The chatbot was trained to assist with complex product-related questions, helping customers check part details, get availability updates, and track their orders without waiting on a human agent.
The Impact: The chatbot now manages over 178,000 conversations per year, fully resolving 37% of all customer chats on its own. This resulted in an 80% reduction in support costs and also led to increased online store conversions, as customers received faster, more accurate answers. Boosting confidence and speeding up the buying process.
Sales Rep Performance Insights – GE
The Situation: General Electric (GE) needed a more efficient way to monitor sales performance across various regions and product lines.
The Chatbot Fix: GE deployed AI chatbots integrated with their CRM systems, allowing sales managers to access real-time performance data through simple queries.
The Impact: This enabled quicker decision-making, personalized coaching for sales reps, and a 15% increase in sales productivity.
The Future of Manufacturing Chatbots
Chatbots have already started making life easier in manufacturing. But what’s next?
The future is about taking them beyond answering questions. Soon, they’ll not only reply faster but they’ll think ahead, help with training, and even take actions for you.
Here are four exciting ways chatbots will become even more useful in manufacturing.
Talking to Chatbots (Voice Assistants)
Right now, most people type their questions into chatbots. But imagine being on the factory floor and just saying, “How many boxes are left in Warehouse 2?” and hearing the answer right away.
That’s what voice assistants can do. You don’t need to stop what you’re doing or use your hands. Just talk, and get instant help.
Why it matters: It’s faster, safer, and more convenient especially when people are working with tools or machines.
Smart Suggestions (Using Generative AI)
In the future, chatbots won’t just wait for your question but they’ll give you helpful tips before you even ask.
Let’s say you manage orders. The chatbot might say:
“Good morning! Last week’s orders from Vendor A were delayed. Want me to follow up?”
Or:
“Product Line B had more returns than usual. Do you want a report?”
This is called generative AI Solution. It looks at your data and suggests what to do next.
Why it matters: It helps managers make better decisions, save time, and stay ahead of problems.
Helping with Training (AR/VR + Chatbots)
Training new employees can be time-consuming. But with new tools like AR (Augmented Reality) and VR (Virtual Reality), it’s getting easier.
In the future, employees might wear smart glasses or a VR headset. The chatbot inside could guide them through tasks step by step.
For example, it might say:
“Look left. That’s the emergency button. Want to see how it works?”
The person says “Yes,” and the demo video plays.
Why it matters: It makes learning faster, more interactive, and doesn’t always need a trainer by your side.
Doing Tasks for You (Conversational RPA)
Right now, chatbots give answers. But in the future, they’ll also take action for you.
Let’s say you tell the chatbot:
“Send a delay notice to the supplier for Order #1001 and update the CRM.”
This is called conversational RPA (Robotic Process Automation). It helps you get things done through simple conversations.
Why it matters: It saves time, reduces errors, and lets people focus on more important work.
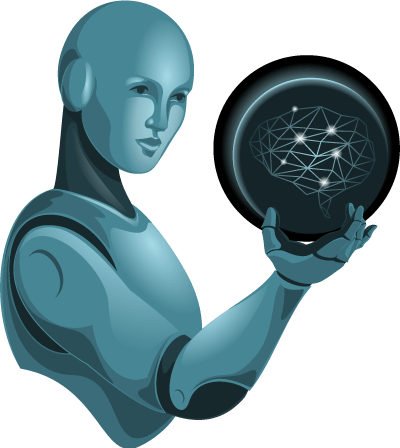
Seeking brilliance in the AI/ML universe?
Look no further!
Conclusion
AI chatbots are no longer just a nice-to-have but they’re quickly becoming a key part of modern manufacturing. They help teams work faster, reduce errors, and make better decisions by turning complex systems into simple conversations. From tracking inventory to helping HR and sales teams, they remove everyday friction and free people up to focus on what really matters. With tools now smarter, more affordable, and easier to connect with your existing systems, this is the right time to explore how chatbots can fit into your operations. Whether you’re just getting started or ready to scale, taking that first step now could set your factory up for a smarter, more efficient future and that’s exactly where Aglowid can help.